Manufacturing Process
Coco Peat
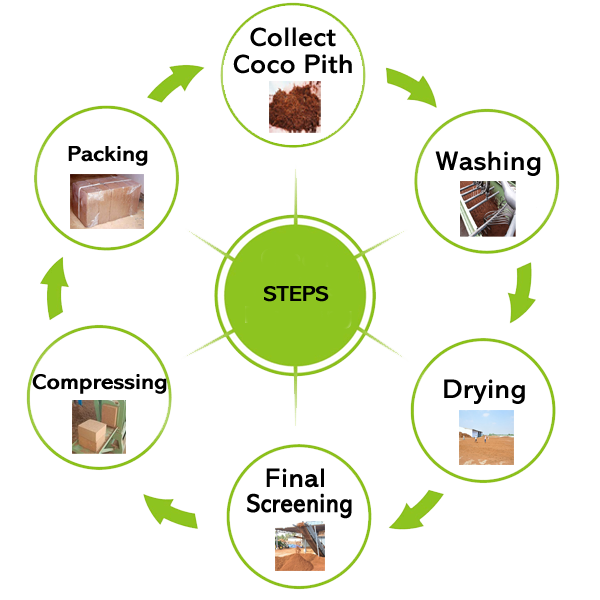
Coco Pith Procurement
Our production process starts with the procurement of freshwater grown coconut husks. The curing process for the coconut husk take over 6 weeks, after this process the coconut fibers are separated and graded. Only the top graded coco pith is used in our products.
Washing / Aging
The top graded coco pith is left in a clean weed free cement floor for over 18 months. During this time, the monsoon rain washes off excess salts from the coco pith and make the coco pith pH neutral. The coco pith is also washed with fresh water to bring the pH and Electric Conductivity (EC) to desired level.
Screening / Sieving
Washed pith is examined for its pH value, Electric Conductivity (EC) and salt content. Once the pith reached the preferred level of EC and pH, it is brought for sieving. During the sieving process, the fiber chunks and other impurities are removed. Once we have the pith to the required sieving size, the material is further sent for drying to reduce moisture content.
Drying
After sieving, the coco pith is dried under the sun on cement floor. Once the moisture of coco peat become below 18%, the coco pith is sent for final screening.
Final Screening
In the final screening / sieving process, the sand is removed by using our screeners. Since it's the final screening process, the coco peat is thoroughly tested for any impurities or bigger coco husks.
Compression
The screened and dried coco peat will be compressed to 5 KG blocks, 650gm bricks, grow bags using our modernized and full automated hydraulic compression machines. The operation teams make sure the right compression ratio is maintained for all our product lines.
Packaging / Labelling
The compressed coco peat blocks & grow bags are tested for visual defects and weight before labeling and packing them individually. Each product / customers have unique packaging requirement whether it's a primary, secondary or tertiary packaging.
Palletizing
After the final inspection of the packaging, the products are palletized as per the shipping standards using the best palletizing materials. Our wooden pallet bases used for packaging are treated in accordance to ISPM standard.
Shipping
Once the pallets are approved for shipping, then the pallets are loaded in truck by registered logistics providers, to be taken to one of the ports in South India. Once the containers are placed on the ship, we track the movement of the vessels and keep our customers updated.
Coconut Coir Pot
Starting from separation of coir fibres from coconut husks to packing of finished coir pots, the coir planter undergoes several steps in the making. With gardening industry blooming into a larger full-scale industry, the pots are also being machine made to match the demands. But a typical handmade coir pot would undergo the following process.
- Separation of coir fibres from the coconut husks
- Removal of coir granules by tossing the fibres in a drum
- Washing of the coir with fresh water and air drying it
- Treatment of coir with steam to a temperature of 50ºC to remove unwanted bugs and weed seeds
Over this period the fibres of the husk become separated giving out stronger fibres that can be used for pot making. The fibre is formed into pot shapes by being pushed into various sizes of pot moulds. Finally, the pots are dunked in latex to make then sturdy and then dried in the sun to be packed and delivered to your garden. There is a wide variety of pot shapes available such as square pots, round and cylindrical pots and hanging coir planters
Areca Disposable Plates
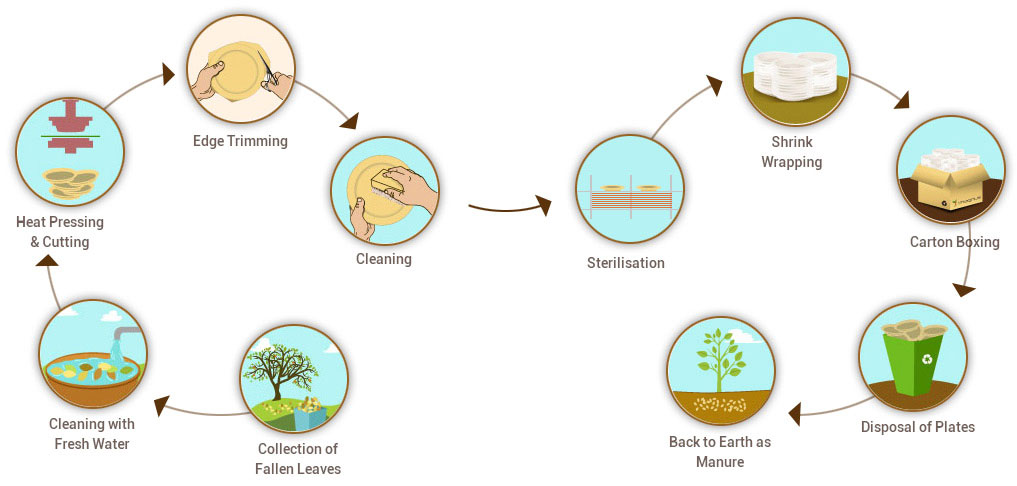
As an Areca leaf product manufacturer, we have set our products to meet international quality standards through optimized manufacturing process with Hygienic conditions, trained and skilled operational personnel and dedicated quality assurance systems.
There are no chemicals or additives used in the entire manufacturing process. It is 100% chemical free. Also the entire process leaves very less Carbon Foot Print when compared to other disposable alternates in the market
Even the water used for cleaning is collected and irrigated for the Green cover in the factory premises.
Our products are manufactured from fallen dry sheaths of Betel nut trees. The areca sheath when dried will fall from the tree and it is collected from the farms fresh and used for making products. These sheaths are available in plenty in the South India region. The usage of these leaves was started from our ancestors. We are only making them into attractive shapes to meet the different customer requirements.